FMECA
03
February,
2023
4 MINUTE READ
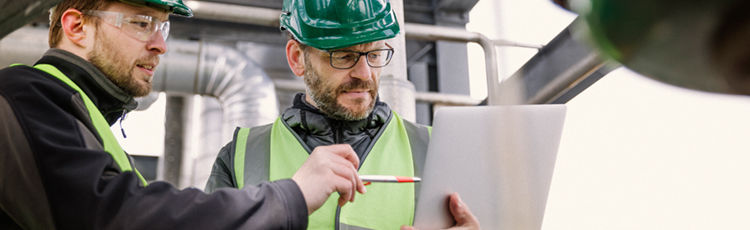
The Fundamentals of FMECA
FMECA is used to evaluate reliability and identify the most critical failure modes. It systematically examines potential failure modes in a system, as well as the components of the system, to determine the impact of a failure. Each potential failure mode is analyzed and given a numerical ranking based on its effects on the system, people, and the environment. The ranking is called a Risk Priority Number (RPN), and is determined by multiplying the rankings for the severity, the likelihood of failure, and the ease of detection of the failure. The RPN is used to prioritize failure modes for remedial action.
The basic procedure is:
- Map the process or system to determine what the system consists of and how it functions.
- Go through the system, step-by-step, to determine potential failure modes.
- Determine the consequences of each potential failure mode
- Determine the likelihood of each potential failure.
- How easy is it to detect the failure? Can the failure be predicted?
- What is the RPN (Consequences X Likelihood X Detectability)?
To calculate the RPN, each of the three components of the calculation are ranked on a scale of 1 to 10.
- How severe is the impact on the customer? (1 no impact / 10 very severe impact)
- How often is the problem likely to occur? (1 rarely / 10 commonly occurs)
- How easy is it to detect the problem? (1 very easy to detect / 10 difficult to detect)
At this point a Failure Mode and Effects Analysis is complete. The final step in FMECA is to perform a Criticality Analysis.
A standard methodology for determining the consequences of an event is via failure modes, effects, and criticality analysis (FMECA), a tool for identifying or investigating potential failure modes and related causes. FMECA can be applied in the early concept selection or design phase and then progressively refined and updated as the design evolves. This type of analysis is helpful in identifying all possible causes, including root causes in some cases, and in establishing the relationship between causes." identifying or investigating potential failure modes and related causes. FMECA can be applied in the early concept selection or design phase and then progressively refined and updated as the design evolves. This type of analysis is helpful in identifying all possible causes, including root causes in some cases, and in establishing the relationship between causes.
FMECA vs. FMEA ? The Criticality Analysis
The difference between FMEA and FMECA is that FMEA is a qualitative analysis based on "what if" questions and human judgment as a means to rank the consequences, likelihood, and detectability of a potential failure. FMECA builds on FMEA to develop limited quantitative analysis using information that can be measured ? the actual failure rate and the severity of the failure. This is called a Criticality Analysis (CA). In addition, FMECA looks at failure modes in more detail, not only looking at the potential failure of components, but also the various failure modes that may lead to a component failure. The contribution of each of these, to the overall failure of the component, is determined and evaluated.
A FMECA Criticality Analysis ranks potential failure modes in order of importance, according to the failure rate and the severity of failure. There are two ways this is done:
- calculate a criticality number
- create a criticality matrix
The criticality number is similar to the RPN, but it provides a more accurate ranking.
Calculating criticality numbers is typically done using actual failure rate data. However, there are situations in which failure rate data is not available. In those cases, the failure modes are assessed for likelihood and severity, with the effect on the overall failure rate assessed subjectively. The calculations are done using the subjectively obtained numbers. This is called a qualitative criticality analysis.
When specific measurable data is available, including the probability of failure and the portion of a component's failure likelihood that can be attributed to each failure mode, then the actual data is used to calculate the criticality number. This is called a quantitative criticality analysis.
The objective is to identify those failure modes with the highest criticality number so they can be addressed first.
FMECA ? Criticality Matrix
Instead of calculating the criticality number, a common approach is to use a Criticality Matrix. A Criticality Matrix is a graphical arrangement of failure modes based on their likelihood and severity. It can be used for either quantitative or qualitative analysis to prioritize failure modes. A Criticality Matrix provides a simple, visual way to differentiate the priority of failure modes with similar criticality numbers.
To create a Criticality Matrix the likelihood and severity are ranked, typically on a scale of 1 to 10, but other scales may be used. The ranking can be done either qualitatively or quantitatively, as long as the approach to ranking remains consistent. For example, a ranking for likelihood might be:
- Rare
- Unlikely
- Occasional
- Probable
- Certain
An example of a ranking for severity would be:
- No impact unable to tell a failure happened.
- Minor is annoying, but the system can continue to operate correctly.
- Marginal results in some system degradation.
- Harmful the system can no longer function correctly.
- Catastrophic may cause injury, death, or extensive damage to the equipment or environment.
Each failure mode is placed on a chart that has increasing severity on the "Y" axis and increasing likelihood on the "X" axis. Those failure modes that fall within the upper right quadrant are the ones that need to be addressed first.
A diagonal line can be drawn from the origin to the upper right corner of the chart. Failure modes located to the right of the diagonal line, because of the high level of severity, are more likely to involve injuries or damage to equipment or the environment. These are more safety related. Items to the left of the line have a higher failure probability, and typically there are greater financial costs associated with them.
FMECA
The objective of FMECA is to provide a more accurate analysis of potential failure modes and to identify those failure modes that are truly the most critical. This is accomplished by examining potential failure modes in more detail than done in FMEA, and either calculating a criticality number and ranking the failure modes or placing the failure modes on a chart called a criticality matrix.
RELATED RESOURCES
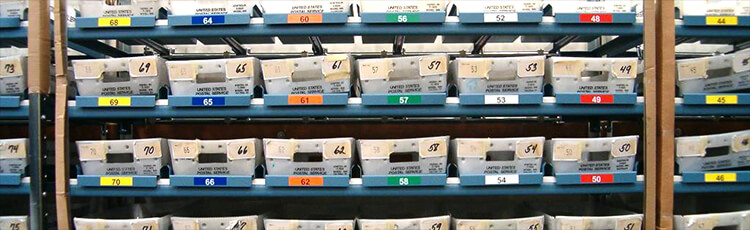
What Is Lean Manufacturing
Lean is an efficient approach to running a process, business or organization to minimize waste, lower lead ...
Read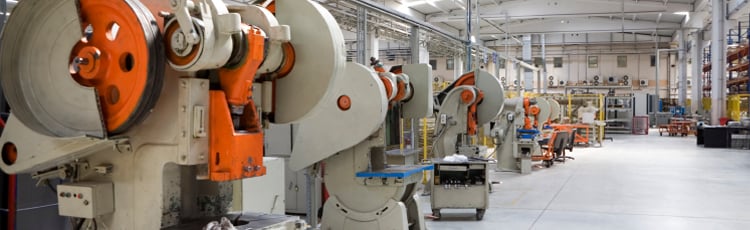
Lean Logistics Techniques
Any successful logistics system needs to provide the required materials where and when they are needed. Lean ...
Read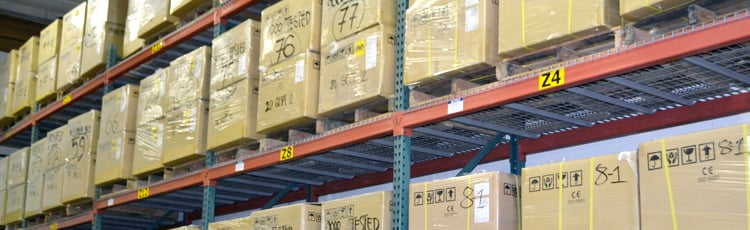
Inventory Planning
What is Inventory? The word "inventory" can have a number of definitions. In this article, we'll be talking ...
Read