Kaizen Event
03
February,
2023
6 MINUTE READ
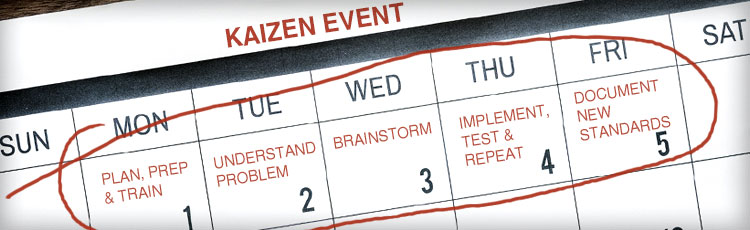
Although they use the same term, a "Kaizen Event" is very different from "Kaizen." While the foundation of Kaizen is making numerous small changes with a goal of continual improvement, a Kaizen Event is a one-time, three- to five-day accelerated process, with a goal of making big changes in a specific high priority area that needs improvement.
The similarity between the two is in the types of improvements that they make. Both approaches aim to eliminate waste, improve productivity, and sustain the resulting changes through the use of standards.
Kaizen, or continuous improvement, refers to a philosophy-a way of thinking and behaving. It's about empowering and unleashing the creative power of people who actually do the work, in order to design more effective and efficient processes-and not requiring leadership's hands-on involvement in doing so.
Kaizen Events, on the other hand, are formalized activities that organizations use to achieve rapid and dramatic improvements (kaikaku) and progressively shift their culture. Kaizen events create a structured environment in which teams learn how to identify waste and apply specific tools to eliminate it.
The Right Tool for the Right Job
A Kaizen Event is not always the right tool. Other approaches may be more effective, depending on the problems that need to be addressed.
In some cases, the three- to five-day time frame of a Kaizen Event simply isn't enough time to properly address the problem. A Kaizen Event is not the right choice when data must be collected over a long period of time before and after any changes. This process may take months to complete, and may need to be repeated afterward.
When the solution to a problem is a capital project, a Kaizen Event is not an effective substitute. If a 60-year-old boiler is providing poor fuel efficiency and high particulate emissions, the solution will likely involve replacing or heavily modifying the boiler, and possibly adding entirely new components. This is not the type of problem that can be effectively addressed by a Kaizen Event.
This is part 2 in our Kaizen educational series for businesses:
- What is Kaizen?
- Kaizen Events, Explained
- Benefits of Kaizen
- Getting Started with Kaizen
- Motivate workers & become a more effective leader with Kaizen (Get our Kaizen Guide)
A Kaizen Event is appropriate for solving problems that can be addressed by a dedicated team within a time frame of one week or less. Since the best solution may not be apparent at the beginning of the Kaizen Event, the event may only identify the root cause of a problem, leaving the actual solution to a long-term engineering or project team.
Purpose of a Kaizen Event
The goal of a Kaizen Event is to eliminate waste and focus on doing the things that make changes a customer values. There are seven basic types of waste to be targeted:
- Defects ? with reliable processes, both defects and quality inspections can be eliminated.
- Waiting ? eliminate the wastes of equipment downtime, lost man-hours, and stock-outs.
- Inventory ? reduce work-in-progress, finished product, and raw material inventories.
- Overproduction ? producing more than is needed results in excessive machine wear, and increased costs for product inventory.
- Over-processing ? don't spend effort to add features that the customer isn't willing to pay for.
- Transportation ? move materials and supplies around as little as possible.
- Unnecessary Motion ? eliminate unneeded effort on the part of employees.
Kaizen Event Steps
Typically, a Kaizen Event begins with a problem already defined, or with a process, product, or area that may need improvement already identified. Areas targeted by Kaizen Events might be:
- Products or processes with substantial work-in-progress.
- Areas where there is a significant bottleneck or delay.
- Areas where "everything is a mess."
- Products or services for which quality or performance does not meet customer expectations.
- Any area that has a significant market or financial impact.
The Kaizen Event follows four basic steps:
- Select team members and set a time and place for the Kaizen event.
- Examine and map the process to be improved.
- Develop ideas for improvements.
- Implement the improvements, and evaluate. (This may send you back to step 3.)
The following is a broad outline of what might typically happen during a five-day Kaizen Event, divided by days. All the team members are expected to be dedicated to the Kaizen Event, and should not be involved with their normal day-to-day activities for the duration of the Kaizen Event.
Kaizen Event Day 1: Planning, Preparation, and Training
The first day is a day of planning. Multi-disciplinary teams, including some experts in the area being targeted, come together in a single location. Generally, the team members should be familiar with the process of a Kaizen Event. However, there may also be a team member or two without experience in Kaizen Events, there to see how such an Event works in real life. One of the purposes of a Kaizen Event is to develop and train others in how to do Kaizen Events.
On the first day, the scope and goals of the Kaizen Event are defined. If there are people who are not thoroughly familiar with the product or process, then training and familiarization is conducted. This typically involves a "gemba walk" through the area being targeted; the Kaizen Event team goes to the real place, or the gemba, where the work is done, in order to get firsthand information.
Kaizen Event Day 2: Understanding the Problem
The team first works to develop a clear understanding of the current state of the targeted process, so that all team members have a similar understanding of the problem. Information to be collected about the targeted area may include:
- Measurements of overall product quality
- Measuring the scrap rate and identifying the source of scrap
- Identifying the routing of materials, supplies, and products
- Measuring the total distance that materials, supplies, and products are moved
- Amount of space used by the required equipment
- Amount of space used for inventory related to the process being studied
- Amount of work-in-progress
- Number and frequency of changeovers
- Identification and source of bottlenecks
- Level of staffing needed for specific tasks
Kaizen Event team members are assigned specific areas of investigation as a part of this research and analysis phase. A map of the process may be created using SIPOC, marking the Sources, Inputs, Procedures, Outputs, and Customers. Time studies may also be appropriate for determining talk time and lead times.
A technique that is commonly used to help fully define a system or process, and identify sources of waste, is the "Five Whys." This technique developed as a part of the Toyota Production System (TPS), and involves asking "why" five times in order to reveal the root cause of a problem. For example:
- Why are the lights out? There was an overload, and the fuse blew.
- Why was there an overload? Too many devices were connected to the circuit.
- Why were too many devices connected to the circuit? The office was cold and people were using space heaters.
- Why was the office cold? Cold air is leaking in through the windows.
- Why is cold air leaking through the windows? Ralph retired and no one else thought to seal the windows this year.
As more information is collected, a more complete Value Stream Map may be developed. Value Stream Mapping involves making a flow chart to show the procedures, material flows, communications, and other activities that take place in a system. Value stream mapping helps identify waste, because it points out activities or inputs to the process that do not add value.
Kaizen Event Days 3-5: Brainstorming Solutions, Implementing, Testing, & Repeat
Once data is gathered, it is analyzed and assessed to identify waste and find areas for improvement. Team members identify and record all observed waste. With knowledge of the process' goal, they can evaluate each step's value. Once waste, or a non-value-added activity, is identified and measured, team members brainstorm improvement options.
The concept of "gemba" is important. Ideas are not just imposed from a distance; instead, the Kaizen Event team needs to go to the real place where the work is done. There, ideas can be discussed with the people actually involved in the process. Those ideas are often tested on a small scale, or in a limited part of the process; separate "mock-ups" are sometimes created and used for testing.
The ideas that are determined to be the most promising are selected and implemented, the results are observed and recorded, and the overall savings are calculated. Savings result from several factors:
- Elimination of waste
- Reduction of operator motion
- Less movement of parts and components
- Less space occupied
- Decreased production time
Kaizen Event Day 5: Documenting the New Standards
A key component of Kaizen is standardization. Written standards are used to document the new, less wasteful way of doing things. Standards also ensure the new work practices and procedures continue to be used in the future. They communicate the improved methods for use in other locations where the same process is used. They also provide a documented base-line for making additional improvements.
Event Follow-Up
Once a Kaizen Event is completed, don't just walk away and forget it. Follow-up (a feedback loop) is a necessary component. Follow-up is used to ensure the standards created by the Kaizen Event are being followed, and that they are delivering the expected benefits. Team members who are doing follow-up measure and record details that characterize the process and expected improvements. They also talk with those involved in the process to get their evaluation of the changes and identify any unintended consequences. The objectives are to document the improvements, ensure the new standards are being followed, and identify areas for further improvement.
Typically the follow-up takes place 30 to 90 days after the end of the Kaizen Event, with the results of the follow-up posted so that everyone can see how well they are doing.
Kaizen Event Labels & Signs
Visual communication, using labels and signs, is used throughout a Kaizen Event, and to implement and sustain the changes resulting from the Kaizen Event. That's why DuraLabel is an important part of Kaizen Events. With a DuraLabel custom label printer, and tough-tested DuraLabel supplies, you'll have the labels and signs you need to:
- Mark and identify physical locations in a process
- Identify test points and procedures
- Communicate changes in standards and procedures
- Inform workers about changes that impact safety
- Communicate the results of the Kaizen Event and the follow-up testing
Overall, labels and signs help reduce injuries and improve workplace safety. DuraLabel industrial label and sign printers by Duralabel can help you develop clear, custom visual communication. With a variety of printers and more than 50 specialty supplies, you'll find the right tools for your needs.
RELATED RESOURCES
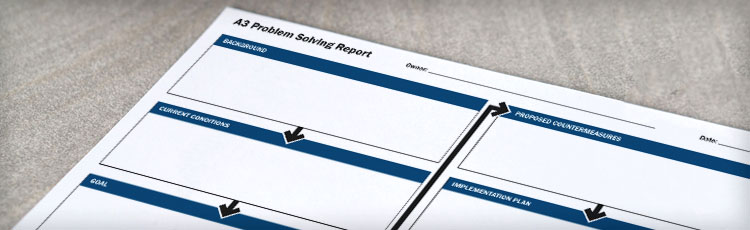
A3 Problem Solving
What is A3, and what does it have to do with problem solving? A3 is a standard paper size, roughly 11"x17" - ...
Read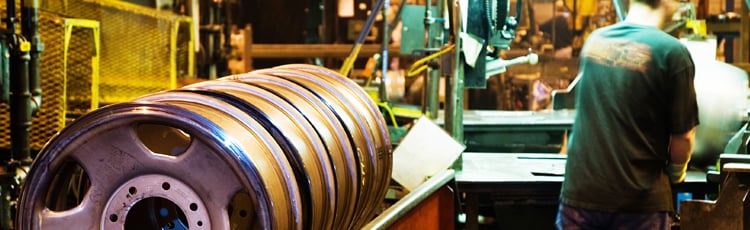
Quality Control In Manufacturing
In manufacturing, quality control is a process that ensures customers receive products free from defects and ...
Read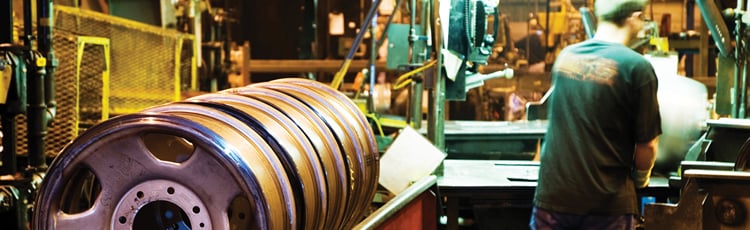
Using Lean Kaizen Theory in Manufacturing
What is Lean Kaizen? From the corner office to the production floor, Kaizen requires all employees to be ...
Read