Kosu
03
February,
2023
3 MINUTE READ
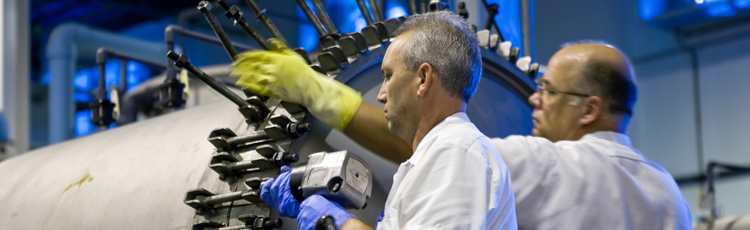
Understanding Kosu
You've implemented a number of lean manufacturing techniques such as 5S and Total Productive Maintenance (TPM), and Kaizen is resulting in a steady flow of suggestions. But, how do you know all of these changes are actually having a beneficial impact? That requires measuring and documenting processes before and after a change, as well as on a long term basis. A lean tool for doing that is kosu.
What is Kosu?
Kosu is a measure of productivity. It refers to the number of man hours it takes to produce one unit of a product, or to complete a process. It is calculated by multiplying the number of workers involved in making a product by the number of hours used. That gives the total man hours. That number is then divided by the total number of units produced during that time.
A Kosu Example
Let's say that you own a widget factory. Yesterday, during a normal eight-hour workday, your factory made 100 widgets. Your factory employs 15 people who are directly involved with making widgets, and 25 people overall. How is kosu calculated? The formula is:
(Number of People X Hours Worked) / Number of widgets made
Putting in the numbers we get:
(15 x 8) / 100 = 1.20
If production increases to 120 widgets per day, then the kosu is:
(15 x 8) / 120 = 1.00
The lower the kosu the better the productivity.
The total overall productivity of the entire factory can also be measured. In our original example the calculation for the entire factory would be:
(25 x 8) / 100 = 2.00
If Bob in accounting, who comes into work at 10 AM, and sleeps most of the day, is fired, the new kosu for the overall factory would improve:
(24 x 8) / 100 = 1.92
Potential Problems of Calculating Kosu
Decisions based on kosu should not be made using numbers collected during a short period of time. There may have been equipment problems, or some employees may have not been feeling well. With kosu you need to look at averages over a significant period of time. The length of that time period depends on what is being produced. If you own a pencil factory making 100,000 pencils per day, then measuring hourly productivity may be reasonable. If your company builds three bedroom homes, then you will be looking at periods that are months long.
Drops in productivity revealed by kosu are not always related to people. Kosu is a tool that allows productivity to easily be measured, but it does not reveal anything about the causes of a change in productivity. For example, if your pencil factory is now making 95,000 pencils per day instead of 100,000 pencils per day, the problem might be that one of the machines needs maintenance, or possibly your suppliers are not delivering raw materials fast enough. Or maybe sales are dropping, the warehouse is full, so production is slowing.
When kosu shows a change in productivity, whether a decrease or increase, the root cause needs to be identified. Using a technique such as the "Five Whys" is often helpful in identifying the root cause. However, you must be talking with the right people. That's why gemba is also important.
Gemba Kosu
The term "gemba" is often combined with kosu. Gemba refers to the physical place where the work is done, such as the location where a product is assembled. Gemba is an important principle in lean manufacturing. If you are truly going to know what is happening, you need to go to the place where it is happening.
When combined with kosu, gemba means that you need to know more than the numbers. The kosu number may be down (improved productivity) or up, but discovering the reason ? the root cause ? involves going to the place where the work is done.
The "Five Whys" involves asking the question "Why?" five times. Let's say that the last step in making a pencil involves adding the eraser. Go to the machine that adds the eraser and ask the machine operator:
- Why has production decreased to 95,000 pencils per day?
- Answer: Because we are only receiving 95,000 pencils from the painting machine.
Practice gemba again and go to the pencil painting machine and ask:
- Why are 95,000 pencils being painted instead of 100,000?
- Answer: Because we are not getting good paint quality when we run the machine faster.
- Why is the paint quality not good?
- Answer: The pressure at the paint nozzle is too low.
- Why is the pressure too low?
- Answer: The pump is not able to deliver the required pressure.
- Why is the pump not able to deliver the required pressure?
- Answer: Because the drive shaft is slipping.
While this is a very simple example, and getting to the root cause may sometimes require asking "why?" more than five times, it shows the principle of going to the location where the work is done and asking "why" until the root cause of the problem is identified.
Include Labels and Signs as Part of Kosu
Labels and signs are valuable communication tools that can be used with kosu. A simple example is posting the kosu numbers for each production station, line, or process. This allows employees to easily see how they are doing, and it may inspire some friendly competition. But, keep in mind that directly comparing kosu numbers for different products or processes is not valid, because the number of units made per man-hour will vary based on what is being produced.
RELATED RESOURCES
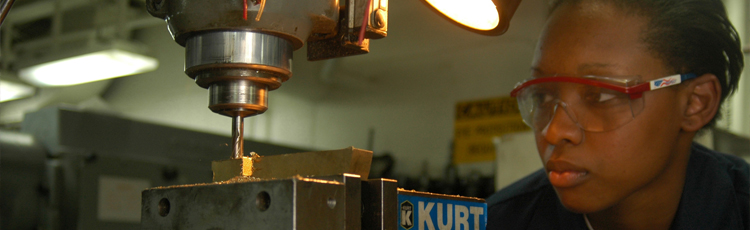
Process Cycle Efficiency (PCE)
The Process Cycle Efficiency, sometimes referred to as the "Value Added Ratio," is a measurement of the ...
Read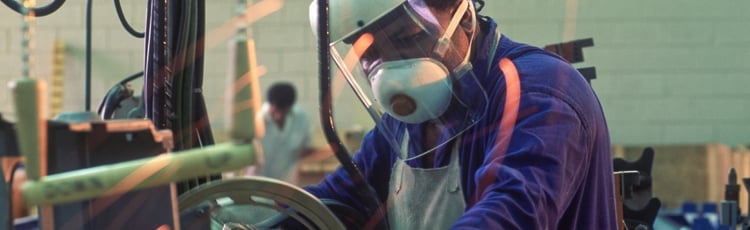
Toyota Production System
What Is the Toyota Production System? Toyota's lean production system has transformed the manufacturing ...
Read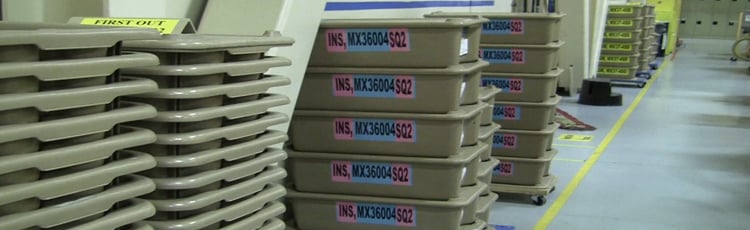
What Is Kanban?
In the face of declining sales and profits during the 1950s, Eiji Toyoda began looking for ways to improve ...
Read