Materials Handling Equipment
03
February,
2023
4 MINUTE READ
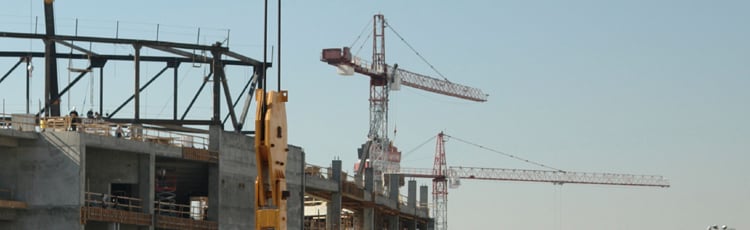
Last month, a New York City window cleaner fell over 30 feet to his death in midtown Manhattan. He fell after stepping off the platform of his 66-foot boom lift to finish cleaning a window before anchoring his lanyard to anything. This tragedy does not stand alone; every year hundreds of workers are killed and thousands more are injured in incidents involving Materials Handling Equipment (MHE). MHE is an umbrella term used to encompass any worksite vehicle so long as it isn't classified as a farm vehicle or powered by compressed air. Vehicles include all cranes, derricks, helicopters, slings, forklifts and any other devices used to move, store and control goods or products throughout the manufacturing or distribution process. Regulations for the safe use, maintenance, and storage of MHE can be found under subpart N of OSHA's 1910 General Safety Regulations
Subpart N covers a lot of ground. First, it provides general guidelines for the safe storage of MHE. Next, it follows detailed regulations for the maintenance and servicing procedures for all types of wheels used on MHE. The subsequent sections are devoted to the care and operation practices of specific types of MHE such as cranes, crawlers, derricks, helicopters and slings.
Understanding the entirety of the guidelines and specifics of training programs required for different MHE in subpart N can be confusing. In 2013, OSHA issued over 700 citations for competency training and 377 citations for lack of certification of training. Beyond citations, it is estimated that between 20 - 25% of accidents involving MHE are caused by inadequate training practices. These citations and accidents are avoidable costs that can be eliminated by giving special attention to MHE training programs and scrutinizing their effectiveness within the workplace.
Training Wheels for Training Programs
When working with any type of MHE, ensuring an operators' competency is priority. The larger the piece of MHE being used, the more extensive training is needed. Much like a semi-truck driver is required to obtain a class A driver's license before hitting the road, many MHE operators must obtain third-party certifications by accredited operator testing organizations before they can go to work. Cranes, for example, have organizations such as the Crane Institute Certification who set up training and certify operators, adhering closely to OSHA standards 1926.1427. It should be noted that despite the training being conducted by a third party, the employer still assumes full responsibility for the thoroughness of the training, the certification of any employees, as well as the subsequent actions of all certified employees.
The most common piece of MHE is the powered industrial truck. Resulted violations ranked number six in 2016 in OSHA's top 10 most commonly cited violations. Forklift and powered industrial trucks cause approximately 100 fatalities and 36,340 serious injuries annually. If ?powered industrial truck' isn't ringing a bell, you might know it by the more common name: the forklift. There are a few other types of powered industrial trucks but because the forklift is so widely used, the two terms have become synonymous. Because of the decreased size and associated destructive power compared to other MHE's, the certifications of forklift drivers is left up to the employer rather than a third party.
When putting a training program together it must consist of three main elements:
- Formal instruction
- Practical training
- Evaluation
Formal instruction should be a lecture, discussion, or interactive computer learning that goes over OSHA standards in detail as well as any situational issues created by the specific workplace. Practical training should be under the direct supervision of a qualified individual who is leading the training. Practical training must be conducted in a place that does not endanger the trainee or other employees. And finally, once initial training or any refresher training is completed, an evaluation of each forklift operator's performance must be conducted.
Training must be conducted by a qualified individual who has a recognized degree, certificate, or professional standing. Knowledgeable forklift dealers, safety companies or consultants will also often provide training courses for a nominal fee, however, it is still the employer who is ultimately responsible for all employee actions.
Once you have a qualified instructor identified, it's time to begin building your program. This is a process that requires employers to complete a long checklist of items in accordance with OSHA regulations that assures the training provided will be thorough. There will be site-specific training for the types of forklifts used as well as any environmental factors that exist. When putting together a training program, utilize OSHA's training program for powered industrial truck operators guide.
Assess and Refresh
Employees must be evaluated on the forklift certification at minimum once every three years. Refresher training and evaluation of its effectiveness are to be administered when any employee is seen operating a vehicle unsafely, involved in an accident, assigned to drive a forklift type they are not trained on, or there is a chance the workplace conditions could affect safe operation.
A largely overlooked part of OSHA's requirements for a refresher course is evaluating the program's effectiveness. In 2013, OSHA issued almost 500 citations for refresher training in relevant topics. Not as tricky as it sounds, OSHA simply wants you to ask the question, "Is this what happens, here?" Get out of the guidelines and really focus on the issues that have been documented or noticed at your workplace. The difference between what is taught in training and practiced on-site can not only cost the company thousands in OSHA fines but can also cost workers their lives.
Here are a few sample questions to get you started when looking at the effectiveness of your training program:
- Are your forklift operations affected by warehouse traffic?
- Are your floors properly marked and taken seriously with floor marking?
- Are the manual and warning labels present and readable?
- Are ALL operators wearing PPE at all times? Even supervisors?
- Has any of your equipment been modified or repaired by a non-certified technician?
- Does your location have any effect on a forklift operators' senses?
OSHA Means Business
Now is the time to form or reevaluate training programs, seeing that OSHA now issues citations on a "per affected employee" basis instead of grouping citations for training and PPE related violations. This means that a $7,000 citation for failure to train forklift operators could become a $210,000 fine if you had 30 operators or trucks out of compliance. Take the necessary steps to form a training program that addresses your facilities needs and achieves overall compliance. It is crucial to take responsibility for the safety and training of your employees to ensure they feel confident and safe in the workplace. Get started with increasing productivity and saving costs facility-wide. Download our free Warehouse Efficiency and Safety guide below.
RELATED RESOURCES

Five Essential Forklift Safety Tips
Forklifts play an essential role in warehouses, retail outlets, and other businesses throughout the United ...
Read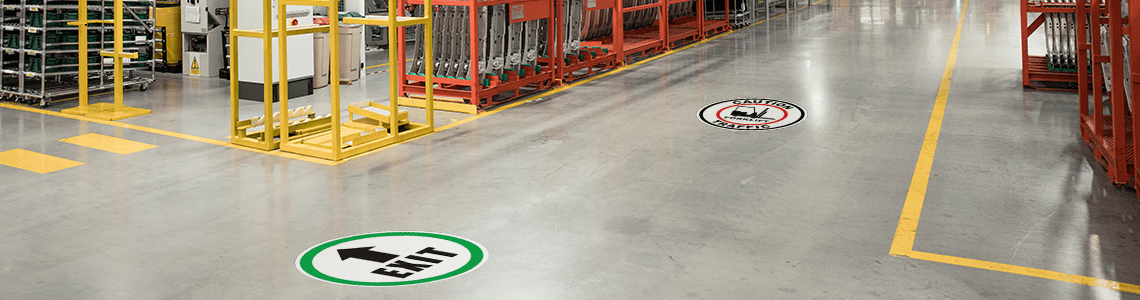
Upgrade Warehouse Traffic Safety with Floor Marking
Modern warehouses experience a wide variety of traffic ranging from forklifts and pedestrians to large ...
Read
Reinforce Safety in Cleanrooms with Floor Tape and More
The typical construction costs for building an ISO 8 to ISO 7 cleanroom can range from $250 to $1,500 per ...
Read