Process Cycle Efficiency (PCE)
03
February,
2023
3 MINUTE READ
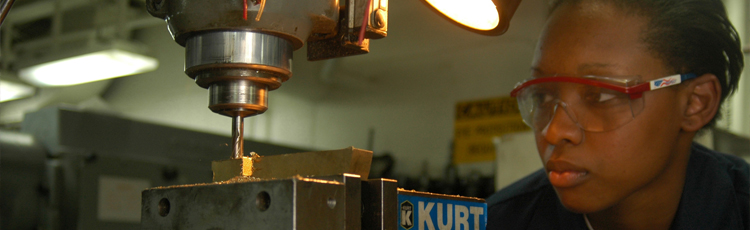
The Process Cycle Efficiency, sometimes referred to as the "Value Added Ratio," is a measurement of the amount of value-added time in a process. The higher the number, the more efficient the process becomes.
Material often spends 95 percent of its time in waiting. This is due to time delay injected by fewer than 20 percent of the workstations known as 'time traps.' We can identify time traps using value stream mapping and eliminate these. The proportion of value-added time is measured by Cycle Efficiency. A Lean process is that in which value-added time in the process is more than 25 percent of the total lead time.
Calculating Process Cycle Efficiency
Calculating process cycle efficiency begins with identifying those areas that do not contribute to the value of the product. This typically can be done using a value stream map, which identifies activities in a process that use resources, time, or space. Those activities are placed in one of three categories:
- Value-added activities ? These add value to the product, meaning they add something the customer is willing to pay for. Always look at value from the viewpoint of the final customer. If the customer would not be willing to pay for an activity, then it is not a value adding activity.
- Necessary, but does not add value ? These are activities that are necessary for producing the product, but do not add value a customer is willing to pay for. For example, I once had lunch in a tech company's cafeteria. Lunch is provided free, and that day featured lobster tails and baked salmon. A customer may not be willing to pay for your employees to have lobster tails for lunch every Wednesday, but you see it as necessary in order to hire and keep talented employees. Although you may consider these activities as necessary, since they do not add value, they are classified as waste.
- Non-value-added activities ? These activities do not add anything of value to the final product. These activities are waste.
There are two important questions: Who are my customers? And what constitutes waste from the customer's perspective?
Who are my customers?
Identifying who is a customer may not always be simple. For example, who are Google's customers? When you use Google to perform a search, are you the customer? No, you are the product Google sells. Google's business is selling advertising. What advertisers buy are clicks on their ads. Google uses its search service to attract people who will click on the ads. That makes you the product Google is selling, and their customers are those who are buying the ads.
What is waste?
Waste is defined as being any of the following:
- Wait-time - idle time when nothing productive is being accomplished.
- Over-Production - producing more than is needed at any specific time.
- Transportation - moving material around without adding value.
- Over-Processing - doing additional work. For example, manufacturing to higher tolerances than the customer requires.
- Inventory - more raw materials, work in progress, or finished products in storage than is required.
- Motion - movement of people that does not add value.
- Defects - not meeting the specifications such that repair or rework is required in order to satisfy customers.
Calculating Process Cycle Efficiency ? Assigning Times
The next step is to determine the amount of time used by each activity on the Value Stream Map. This should equal the cycle time, which is the amount of time required to receive and process an order, through to the delivery of the product to the customer. A common way to calculate the cycle time is to take the total number of paid man-hours in a month, and divide that by the number of finished products produced that month. This gives the amount of time required to produce one item. That time is then divided among the activities on the value stream map.
Process Cycle Efficiency ? The Calculation
The calculation for Process Cycle Efficiency uses a simple formula:
- Process Cycle Efficiency = Value-Added Time / Cycle Time
If the process only includes activities that add value a customer is willing to pay for, then the process cycle efficiency is 100%. We like to think that our processes are close to 100% efficient. That the customer is willing to pay for everything we do in making the product they purchase. In reality the process cycle efficiency is typically in the 5% to 10% range. Once lean methods have been used to improve a process, the efficiency may improve to be in the range of 20-25%.
This means there is always room for improvement.
One of the important aspects of calculating the Process Cycle Efficiency is to establish a standard for how it will be calculated. To know if your Process Cycle Efficiency is improving, you need to be sure it is calculated the same way each time.
Process Cycle Efficiency is improved by decreasing the cycle time through the elimination non-value added activities, and minimizing the necessary, but non-value adding activities. One of the tools for reducing cycle time is Quick Response Manufacturing (QRM). QRM puts the focus on reducing the time from order receipt to product delivery, by eliminating all unnecessary steps and activities.
Process Cycle Efficiency and 5S
Seeing the activities involved in a process, and the amount of time they each require, is made a lot easier when the workplace is well organized. That's why 5S is one of the foundational principles of lean manufacturing. You can learn more about 5S, and how it can help your organization be more productive, with a 5S System Guide from Duralabel.
RELATED RESOURCES
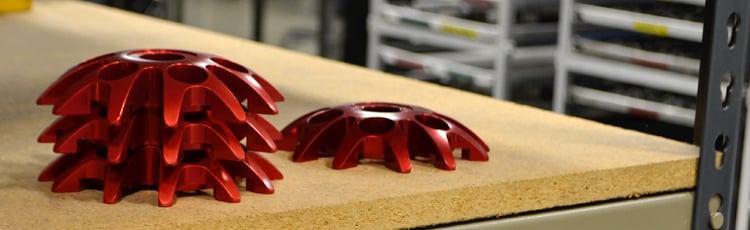
Is Batch Production the Right Production Method for Your Organization?
The Myth of Large-Batch Production Manufacturers of everything from cakes to computer chips have many ways of ...
Read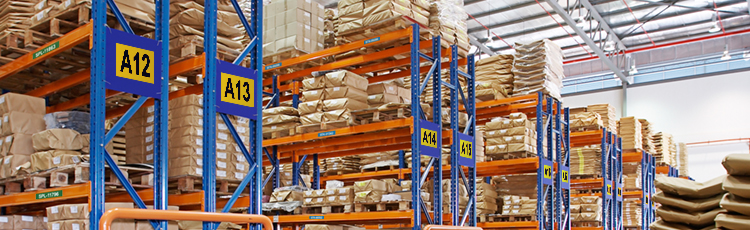
Warehouse Management
The global market is increasingly pressuring businesses to improve the efficiency of their operations. ...
Read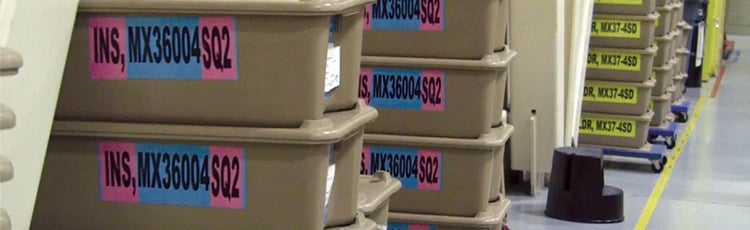
Lean Manufacturing Principles
The Principles of Lean Manufacturing To gain a competitive edge, many companies have adopted lean ...
Read