OSHA 1910 144 Color Identification
03
February,
2023
3 MINUTE READ
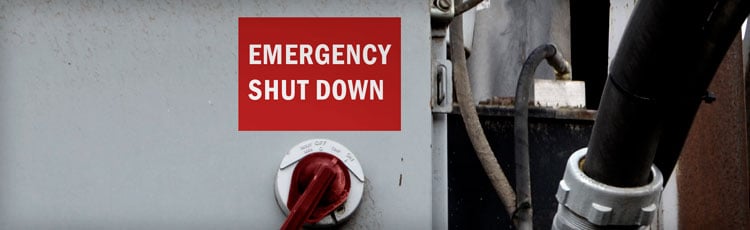
Standard Number: 1910.144
Safety color code for marking physical hazards.
1910.144(a) Color identification -
1910.144(a)(1) Red. Red shall be the basic color for the identification of:
1910.144(a)(1)(i) Fire protection equipment and apparatus. [Reserved]
1910.144(a)(1)(ii) Danger. Safety cans or other portable containers of flammable liquids having a flash point at or below 80? F, table containers of flammable liquids (open cup tester), excluding shipping containers, shall be painted red with some additional clearly visible identification either in the form of a yellow band around the can or the name of the contents conspicuously stenciled or painted on the can in yellow. Red lights shall be provided at barricades and at temporary obstructions. Danger signs shall be painted red.
1910.144(a)(1)(iii) Stop. Emergency stop bars on hazardous machines such as rubber mills, wire blocks, flat work ironers, etc., shall be red. Stop buttons or electrical switches which letters or other markings appear, used for emergency stopping of machinery shall be red.
1910.144(a)(2) [Reserved]
1910.144(a)(3) Yellow. Yellow shall be the basic color for designating caution and for marking physical hazards such as: Striking against, stumbling, falling, tripping, and 'caught in between.'
Use colors to improve response time
Color associations register in the brain before words on signs can be mentally processed. This means that color markings improve response time, decreasing the likelihood of incidents. This OSHA standard mandates red color coding of dangerous items, fire prevention devices, or items used to stop a machine/process, while yellow designates caution or hazard. Most people already associate red with danger/stop/fire and yellow with caution-with some credit owing to the universal familiarity of stoplights.
What is flash point?
OSHA defines flash point as the minimum temperature at which a liquid gives off vapor within a test vessel in sufficient concentration to form an ignitable mixture with air near the surface of the liquid. Simply put, the chemical may ignite at room temperature or below, representing a significant risk. Examples include diethyl ether and acetone, which have flash points significantly below room temperature.
Look to the diamond
Check the NFPA diamond on a chemical's container. Any chemical with an NFPA Fire Hazard rating of 4 in the red diamond has a flash point below 73? F. Since NFPA standards have a different danger range than this OSHA standard, some chemicals with a Fire Hazard rating of 3 may also need to be denoted with red, as these have a flash point below 100? F. If the chemical has a Fire Hazard rating of 3 on the NFPA diamond, check the SDS for the chemical to ascertain flash point.
Does anything impact flash point?
Mixing chemicals with water or other substances may affect their flash point, as in the example of ethyl alcohol. In its pure form it has a flash point of 55? F, while if diluted to 30%, the flash point drops to 85? F and it is no longer defined as dangerous by this standard.
"Open cup tester" refers to the method used to determine flash point. As closed cup testing can result in lower flash points, testing method should be noted while assessing whether this color standard must be invoked. NFPA standards make recommendations about which testing type should be used, based on estimated flash point, viscosity, or chemical type. SDS/MSDS will typically disclose which method was used to ascertain flash point. If closed cup testing was used and the flash point is near 80? F, it is advisable to store the chemical in a red container to assure compliance if retesting is not feasible and open cup testing results are not available for the chemical in question.
What are the risks of these chemicals?
Excessively flammable liquids tend to produce heavier vapors. A lower flash point also increases the amount of vapor produced. These (often invisible) dense vapors may travel great distances, flowing down stairs or shafts. Once ignited, the flame follows its flow path (if the vapor stream is fairly contiguous and intact) back to its original source, possibly causing a container explosion in addition to a rapidly moving line or wall of flame, so it can present a significant risk.
If in doubt about the flash point of the chemical, store it in a red container.
Do any other sections of a machine require color coding?
1910.144(a)(1)(iii) This standard lists the machine sections which mandatorily must be color coded. However any potentially hazardous part of a machine-regardless of whether that particular hazard type is mentioned in this code-must be color coded.
In addition to color coding, are other safety measure required?
Color coding does nor override the need to follow any other standards for compliance; proper machine guarding and lockout/tagout (LOTO) is still required. Signs must not create a separate hazard, by creating a trip hazard, hanging too low, or containing sharp edges or other protrusions.
RELATED RESOURCES
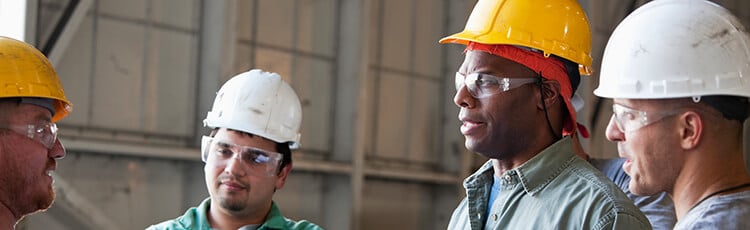
What Is OSHA 10? | OSHA 10 Certification |
The term OSHA 10 refers to the OSHA Ten Hour Training that is part of the OSHA Outreach Training Program. The ...
Read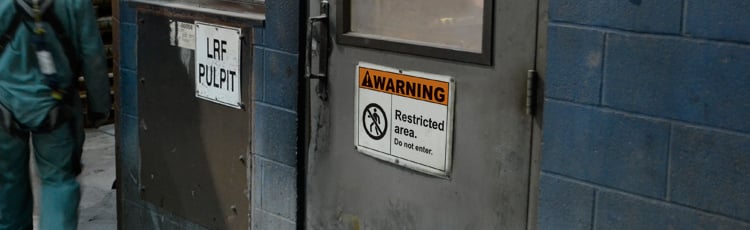
OSHA 1910 145 Warning Signs and Tags
No matter the industry, hazards are rampant in workplaces throughout the United States. Manufacturing ...
Read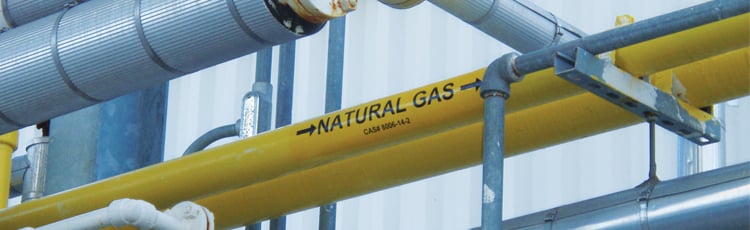
ASME A13.1 | Pipe Marking Guide | ANSI Pipe Labeling |
Pipe marking quickly communicates essential information to everyone in a facility, improving overall ...
Read